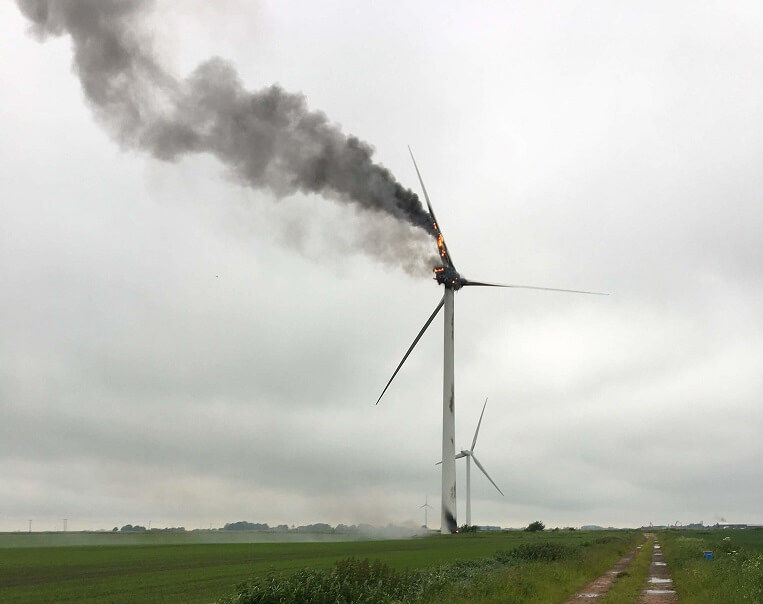
Despite being the second leading cause of reported incidents in wind turbines, the wind industry is still largely overlooking fire risk.
Few sights are more dramatic than that of a wind turbine on fire. Though rare, the spectacle of rotating flames and falling debris live long in the memory.
Even so, despite the high-profile nature of these events, there is little in the way of accurate records detailing the number of turbine fires and the extent of the financial damage they cause. Indeed, these facts tend to be known only by insurers and project owner operators.
On Dec. 29, 2022, the Galgenberg wind farm, in southwestern Germany, suffered the loss of a 2 MW turbine to fire. Investigations into the cause of this fire have so far failed to yield a definitive answer, but the operator, Windpark Saar, suspects an issue with the braking system.
This incident followed hot on the heels of a fire at the Diamond Trail wind farm in Iowa County in late October 2022. This fire, spreading to the field and surrounding environment, caused several turbines to be taken offline and demonstrated the disruption a turbine fire can cause beyond simply the loss of a single asset.
Given that fire is the most likely cause of a reported incident in turbines after blade failure, key stakeholders should ask themselves if they are comfortable with the potential losses incurred by a fire. If the answer is no, then the follow up question should be: Why am I taking the risk when there are tried and proven solutions out there?
Barring a lightning strike in a storm, preventing fires in wind turbines is actually very straightforward once the turbine is equipped with appropriate fire suppression technology. As such, it is accountability, and not opportunity, that is proving to be the real stumbling block when it comes to mitigating this avoidable risk.
The assumption that someone else is responsible for managing fire risk, rather than it being a collective effort, all too often means that no one is managing fire risk at all. Here’s how each group can take responsibility:
Owner operators. Project owner operators play a pivotal role in changing the approach to fire risk management. The common belief among owner operators is that fire risk has been “designed out” at the manufacturing stage. Though OEMs have made great strides in design and safety, high-voltage electrical equipment can and does occasionally fail. Developers are experiencing such time and financial pressures that installing fire suppression technology is not often prioritized. The duty is, then, passed onto the owner operator to either do nothing, or arrange to retrofit the technology once they have completed commissioning.
Unless developers and owner operators are on the same page, the likelihood is that the appropriate technology is never fitted, the risk is never managed and, implicitly, insurers are relied upon to cover the costs if the asset is destroyed by fire.
In the case of the recent event in Germany, the loss of the asset to fire is presumed to have been caused by a braking system failure. This is unexpected given that the model was only seven years old and presumably well maintained. This should serve as an example to owner operators that, though tempting to dismiss turbine fire as an unlikely event, there is always an element of unpredictability that makes installing fire suppression technology essential to defend against the worst-case scenario of a catastrophic fire.
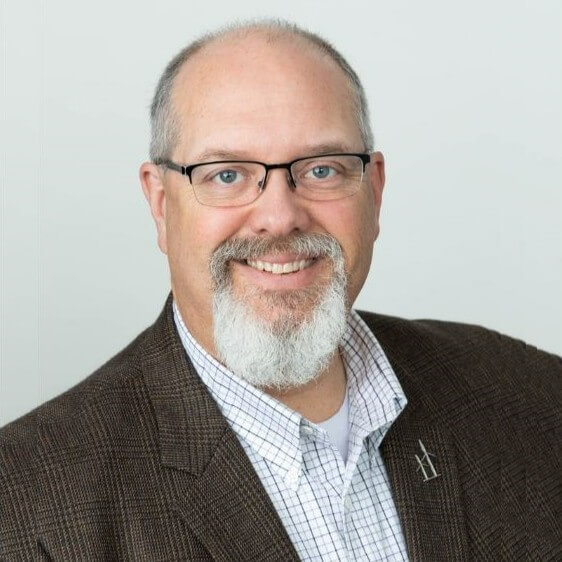
Ultimately, wind turbines are high-voltage machines that are subjected to harsh weather conditions. Degradation and maintenance needs are to be expected. To this end, high-voltage cabinets, transformer rooms, brakes and slip rings are all routinely checked for signs of wear. However, even though it is easy to equip the technology, not all of these parts are protected from fire risk.
Fire incidents on wind turbines are, thankfully, not common. The probability of wind turbine fire ranges between one in 2,000 to one in 7,000. However, the overriding point should be that it is a possibility threatening turbines every year. Owners should not only keep in mind the cost of a lost asset, and downtime, but also significant increased insurance rates after a fire event, which go on for the life of the project. The current practice of retrofitting fire suppression systems only after a fire event, rather than proactively, is unsustainable.
Between owner operators and developers lies the opportunity to address fire risk before it burns a hole in the owner operator’s pocket.
Insurers. If the hardening of the insurance market is anything to go by, insurers are aware of this responsibility vacuum and are acting accordingly, even as more insurance capital floods into the sector. Owner operators who underwriters deem to be ignoring their fire risk responsibilities are at the mercy of increasing premiums.
The loss of an asset to fire exposes insurers to heavy claims. It is not just the potential millions of dollars needed for cleanup and turbine replacement, but also the business interruption during downtime that can amount to as much as $2,000.00 of lost revenue a day. Since the average downtime after a fire is between 12 and 18 months, insurers are looking at extra hundreds of thousands of dollars in additional claims.
With this in mind, the more owners rely on insurers to wear these risks, the more they are inviting insurers to increase deductibles and remove business interruption coverage to re-balance the underestimation of their risk portfolios. Data from GCube show that insurers have seen a 38{7bfcd0aebedba9ec56d5615176ab7cebc5409dfb82345290162ba6c44abf8bc8} increase in business interruption claims since 2016, which would justify such decisions in future.
However, this approach does little to encourage owner operators to take control of the risk themselves. By raising premiums instead of incentivizing the retrofitting, or requesting, of fire suppression systems, there is a concern that this supports the industry attitude that the bill for fire damage belongs to the insurer.
A simple step to actively reduce the volume of annual claims related to fire is to take advantage of the bankable fire detection and suppression solutions that are available to the renewables industry. Plenty can be learned from more mature industries where insureds can expect discounted terms when they adopt proven fire risk-protection technologies.
Policymakers and regulators. While regulation of the wind sector has been fairly lenient in Europe, it is even more so in the U.S. At present, the National Fire Protection 850 code is the sole legislation that wind projects have to comply with – but this legislation applies generically to all forms of power generation and offers recommendations rather than requirements.
Consequently, there is still no obligation that owner operators carry out a fire risk assessment on their wind projects. This, at a time when wind power is set for historic expansion across the U.S. and to become one of the main sources of utility-scale energy, is unacceptably relaxed.
Given the anticipated growth of the industry over the next few years, it is possible that regulators will also introduce uniform guidelines on fire risk. Why wait to be told to manage this risk when you can manage it today?
Ross Paznokas is global business development manager, clean energy, at Firetrace, a company that develops systems designed to detect and suppress fires in multiple applications.
Photo source – Cambridgeshire Fire and Rescue Service | Flickr