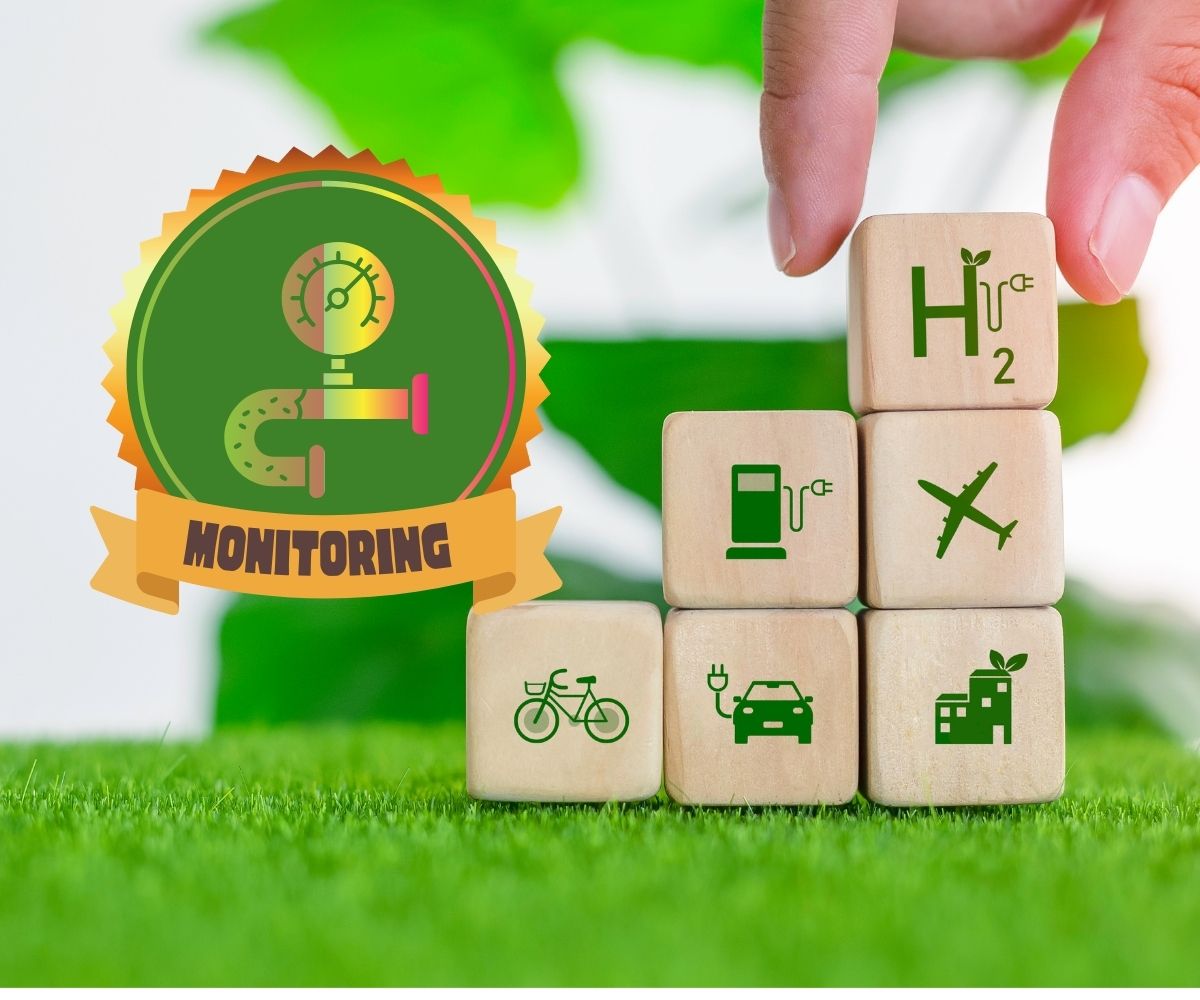
Hydrogen, while a vital component in various industrial processes, poses significant risks due to its highly flammable nature. As industries continue to integrate hydrogen into their operations, the importance of hydrogen monitoring systems becomes increasingly evident. These systems are designed to detect potential leaks, prevent accidents, and enhance the overall safety protocols of industrial facilities. With a better understanding of how hydrogen monitoring works and its various applications, industries can ensure the safe and efficient use of this highly reactive gas.
Continuous Transformer Monitoring
Continuous transformer monitoring is critical in maintaining the reliability and efficiency of power systems. By incorporating advanced hydrogen sensors into transformer monitoring, facilities can achieve real-time data analysis, detecting even the smallest leaks that might pose a threat to the system’s integrity. As explained by H2scan and other reliable online resources and professionals in the field, accurate monitoring aids in the early detection of any anomalies and allows for timely preventative measures, significantly reducing the risk of unexpected shutdowns and costly repairs. These innovative monitoring techniques ensure that transformers operate seamlessly and safely during their service life.
Fuel Cells and Hydrogen Storage
Fuel cells and hydrogen storage solutions are integral components in advancing sustainable energy technologies. As industries shift towards cleaner energy sources, the role of hydrogen as both an energy carrier and storage medium becomes increasingly significant. Proper monitoring of hydrogen within fuel cells is crucial to ensuring operational reliability and longevity.
Through the use of specialized monitoring systems, it is possible to track hydrogen purity, pressure levels, and temperature, critical parameters for the efficient functioning of fuel cells.
These systems help in detecting leaks promptly, thus maintaining the safety of storage facilities and protecting investments. Advances in hydrogen monitoring are paving the way for safer, more efficient fuel cell systems, positioning hydrogen as a cornerstone of future energy solutions.
Alarm Systems
Designed to provide immediate alerts, these systems are integral to a facility’s emergency response strategy. When hydrogen levels exceed predefined safety thresholds, the alarm systems activate, prompting immediate action to address the situation. Equipped with both visual and auditory alerts, these systems ensure that on-site personnel are informed of the potential hazard, enabling quick and effective responses.
The integration of alarm systems with hydrogen monitoring technology enhances their effectiveness, allowing for synchronized data sharing and response coordination. This synergy safeguards the facility and protects the workforce. Note that alarm systems are also essential in preventing accidents related to human error as they act as a failsafe mechanism against complacency.
Regulatory Compliance
Industries utilizing hydrogen are subject to stringent regulations and standards, which dictate the necessary safety protocols and operational benchmarks. Compliance with these standards guarantees the safety of the operations and instills confidence among stakeholders and the public.
Organizations must implement comprehensive hydrogen monitoring solutions to meet these regulatory requirements. These systems provide reliable data to support compliance reporting, evidence of due diligence, and proactive risk management strategies. Furthermore, monitoring systems are frequently assessed during regulatory inspections to ensure their effectiveness in maintaining safety.
Data Analysis and Reporting
By continuously collecting data from various monitoring devices, facilities can gain comprehensive insights into the performance and safety of their hydrogen-handling operations. Sophisticated analytics tools enable the identification of trends and patterns, allowing for predictive maintenance and timely interventions to mitigate potential risks.
Aside from enhancing operational efficiency, these data-driven approaches also support transparent reporting practices. Regular reports generated from monitoring systems provide valuable documentation for audits and regulatory compliance so that facilities can demonstrate adherence to safety standards. The integration of robust data analysis and reporting mechanisms forms the backbone of a proactive and resilient safety culture within industries leveraging hydrogen technologies.
Enhanced Safety Protocols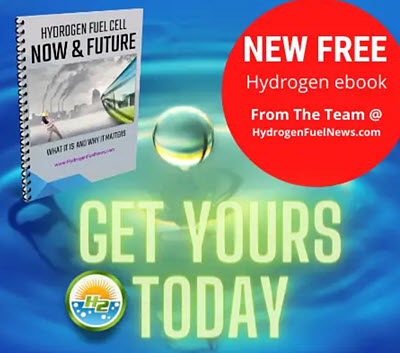
The implementation of enhanced safety protocols is central to the successful integration of hydrogen monitoring systems in industrial applications. These protocols encompass a range of strategies and best practices designed to maximize safety while utilizing hydrogen. Key elements include comprehensive training programs for personnel to ensure they are well-versed in handling hydrogen safely, along with emergency response drills that prepare teams for potential scenarios involving hydrogen leaks or fire.
Safety protocols emphasize the importance of regular equipment maintenance and inspections to prevent failures. By establishing a culture of safety, companies can minimize risks, protect their workforce, and maintain smooth operations even in the face of challenges. These proactive measures contribute significantly to a safer, more reliable use of hydrogen across various industrial settings.
The integration of hydrogen monitoring systems into industrial applications is not merely an enhancement, but a critical necessity for ensuring safety and operational efficiency. The continuous evolution of monitoring technologies underscores the industry’s commitment to embracing hydrogen as a key component of sustainable energy solutions.
By prioritizing safety through state-of-the-art systems, industries can mitigate potential risks associated with hydrogen’s flammable nature, uphold compliance with stringent regulatory standards, and instill confidence in stakeholders. As the quest for cleaner energy continues, the importance of robust hydrogen monitoring frameworks will only grow, resulting in safer industrial processes and a more sustainable future.