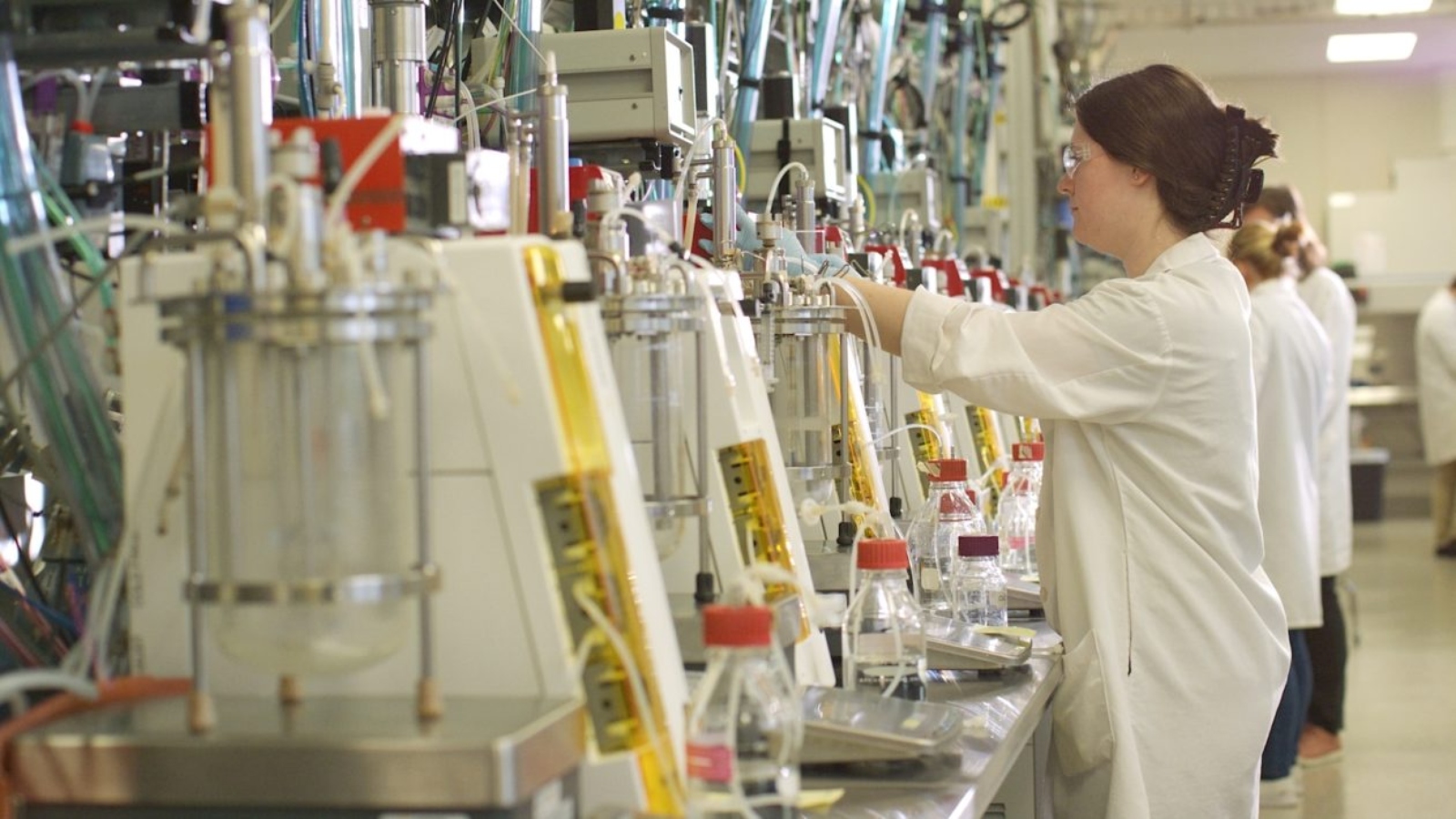
This story was originally published by Yale Environment 360 and is reproduced here as part of the Climate Desk collaboration.
In the 1930s, the DuPont company created the world’s first nylon, a synthetic polymer made from petroleum. The product first appeared in bristles for toothbrushes, but eventually it would be used for a broad range of products, from stockings to blouses, carpets, food packaging, and even dental floss.
Nylon is still widely used, but, like other plastics, it has environmental downsides: it is made from a nonrenewable resource; its production generates nitrous oxide, a potent greenhouse gas; it doesn’t biodegrade; and it sheds microfibers that end up in food, water, plants, animals, and even the clouds.
Now, however, a San Diego-based company called Genomatica is offering an alternative: a so-called plant-based nylon made through biosynthesis, in which a genetically engineered microorganism ferments plant sugars to create a chemical intermediate that can be turned into nylon-6 polymer chips, and then textiles. The company has partnered with Lululemon, Unilever, and others to manufacture this and other bio-based products that safely decompose.
“We are at the start of a sustainable materials transition that will reinvent the products we use every day and where they come from,” says Christophe Schilling, Genomatica’s CEO.
Using living organisms to create safe materials that break down completely in the environment — where they can act as nutrients or feedstock for new growth — is just one example of a burgeoning global movement working toward a so-called bioeconomy. Its goal isn’t limited to replacing plastics but takes aim at all conventional synthetic products — including chemicals, concrete, and steel — that are toxic to make or use, difficult to recycle, and have outsize carbon footprints. In their place will come products made from plants, trees, or fungi — materials that, at their end of life, can be safely returned to the Earth or recycled again and again. The bioeconomy is still small, in the global scheme of things, but the push to turn successful research into manufactured products is growing, propelled by several factors.
First is widespread disgust at the mounting environmental toll of plastic, including the fact that people and animals are ingesting it. Second is a flood of funding, especially in the United States and Europe, to accelerate the transition away from products that are non-biodegradable, toxic, and that produce carbon emissions. Last September, President Biden signed an executive order, with funding of more than $2 billion, to launch the National Biotechnology and Biomanufacturing Initiative to support research and development efforts, including the use of sustainable biomass and waste resources to make non-toxic, bio-based fuels, chemicals, and fertilizers, and to build affordable housing.
MycoWorks
And the Department of Defense recently funded what it calls a Manufacturing Innovation Institute called BioMADE, or the Bioindustrial Manufacturing and Design Ecosystem, a public-private partnership with its headquarters at the University of Minnesota. Bioindustrial manufacturing uses biological systems — including microbes like bacteria, yeast, and algae — to create new materials or alternatives to existing petroleum-based materials. Ongoing projects include the creation of a bacterium, made from byproducts of the dairy industry, that displaces petroleum-based propylene as the feedstock for acrylic acid, which is used to make vinyl, paint, adhesives, diapers, and other products, and a bacterium that safely kills pathogens in chickens, replacing antibiotics.
The U.S. Department of Agriculture is also a major player in this field. The agency recently announced it would allocate $41 million to develop new markets for products made from wood, and it has long managed the BioPreferred Program, which requires federal agencies and contractors to preferentially purchase products, including cleaners, carpets, lubricants, and paints, with minimum bio-based content. Among the products federal agencies are now using is a transformer coolant made from soybean oil that is 99 percent biodegradable in 21 days and Seventh Generation laundry detergent, which is made from 97 percent bio-based ingredients. While the bioeconomy concept has been around for a while, the surge of funding and interest has seeded a range of new facilities and projects. The University of Maine’s Advanced Structures and Composites Center just manufactured a completely recyclable house; the Material Innovation Initiative develops sustainable textiles without animal products. Oak Ridge National Laboratory has the Center for BioEnergy Innovation, which studies fuels made from plants and the bioenergy supply chain.
Across the Atlantic, Horizon Europe, the European Union’s key funding program, has dedicated at least $2 billion to accelerate its own transition to a bioeconomy. The program’s goals are to fund innovative bio-based products to make them a less risky investment, to make sure the new products and systems perform as claimed, and to get them to market promptly.
New regulations governing waste streams are another major driver of this transition. The EU has just proposed new rules to require that all product packaging be recyclable in an economically viable way and possibly reusable by 2030. The continent’s textile industry is also bracing for new sustainability rules. “The fashion industry from the EU’s point of view will be regulated from A to Z within a couple of years,” Rannveig van Iterson, a senior consultant at Ohana Public Affairs, recently told Women’s Wear Daily. “It’s going from basically zero with no sustainability legislation to kind of covering everything from production to design to waste.” The entire process of making clothes, in other words, may soon be required to become bio-based.
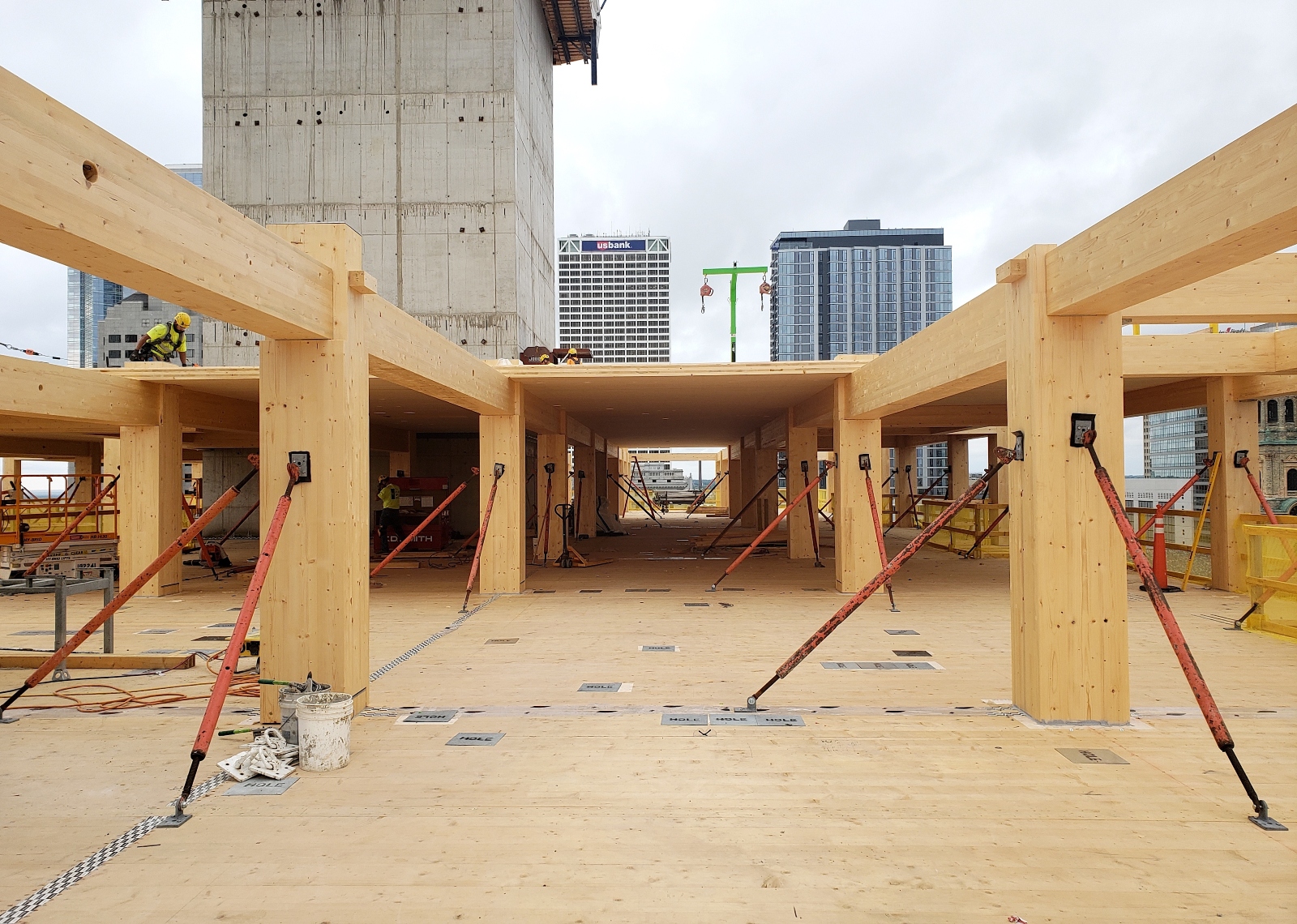
Thorton Tomasetti / Yale Environment360
The fashion industry is under enormous pressure to clean up its act, says Frank Zambrelli, executive director of the Responsible Business Coalition at Fordham University, in New York. The sector produces 92 million tons of waste globally each year, and its CO2 emissions are projected to increase by 50 percent by 2030. Tanning hides for leather requires a number of toxic chemicals, including chrome, formaldehyde, and arsenic. One promising leather alternative comes from mushrooms. In 2016, MycoWorks began producing a leather-like textile, called Reishi, from mushroom mycelium, which one study found has a carbon footprint that’s just 8 percent of bovine leather’s footprint. The company has been wildly successful, and now produces textiles ranging from sheets to canvas to car seats for major brands. Based in Emeryville, California, MycoWorks has more than 160 employees and just broke ground on a 150,000 square-foot plant.
Concerns about looming restrictions have led to a big push to scale up new, safer materials. “There are more and more and more responsible options,” says Zambrelli. “Many of these alternatives have been around for a while, but we are starting to see real investments.”
As more regulations come into play, companies are going to have to take the disclosure of their products’ environmental information in official reporting more seriously, Zambrelli added. “When you’ve got the CFOs [chief financial officers] and general counsels involved in the reporting, suddenly there’s a legitimizing factor in what they are doing.”
In addition to regulatory pressure, said Rob Handfield, who studies bio-based supply chains at North Carolina State University, there is growing pressure from shareholders. “More and more companies now have investors that are requesting science-based targets,” he said. “And there is big customer pressure as well. They are asking companies not only to make a commitment, but to put their money where their mouth is.”
It helps, too, that bio-based products are increasingly profitable. One estimate places the U.S. value of the bioeconomy at $1 trillion and the global value at $4 trillion. A 2020 World Business Council for Sustainable Development report projects that the economic opportunity for bio-based products could grow to more than $7 trillion by 2030.
Rapidly evolving technology is enabling new approaches and products. Plain old low-tech wood — from trees — is getting an enormous amount of attention as a replacement for steel and concrete in construction. (Steel manufacturing contributes about 8 percent of global carbon dioxide emissions, and concrete manufacturing contributes another roughly 8 percent.)
A product called MettleWood, developed at the Center for Materials Innovation at the University of Maryland, is derived from soft wood from commercial plantations that has had its lignin removed. In a proprietary process, the lignin-free wood is then densified under high pressure, creating wood that its maker claims is 80 percent lighter than steel, 20 percent stronger, and roughly half the cost. InventWood, the company that makes MettleWood, just received a $20 million grant from the U.S. Department of Energy to scale up production.
The University of Maine’s Advanced Structures and Composites Center recently showed off a 3D-printed house made from a mix of forest byproducts from the state’s numerous sawmills: sawdust, wood flour (a very fine sawdust), and a bio-resin whose ingredients have not yet been disclosed. The entire envelope of the house — walls, floor, and roof — is printed from wood fibers and bio-resins and insulated with 100 percent wood insulation.
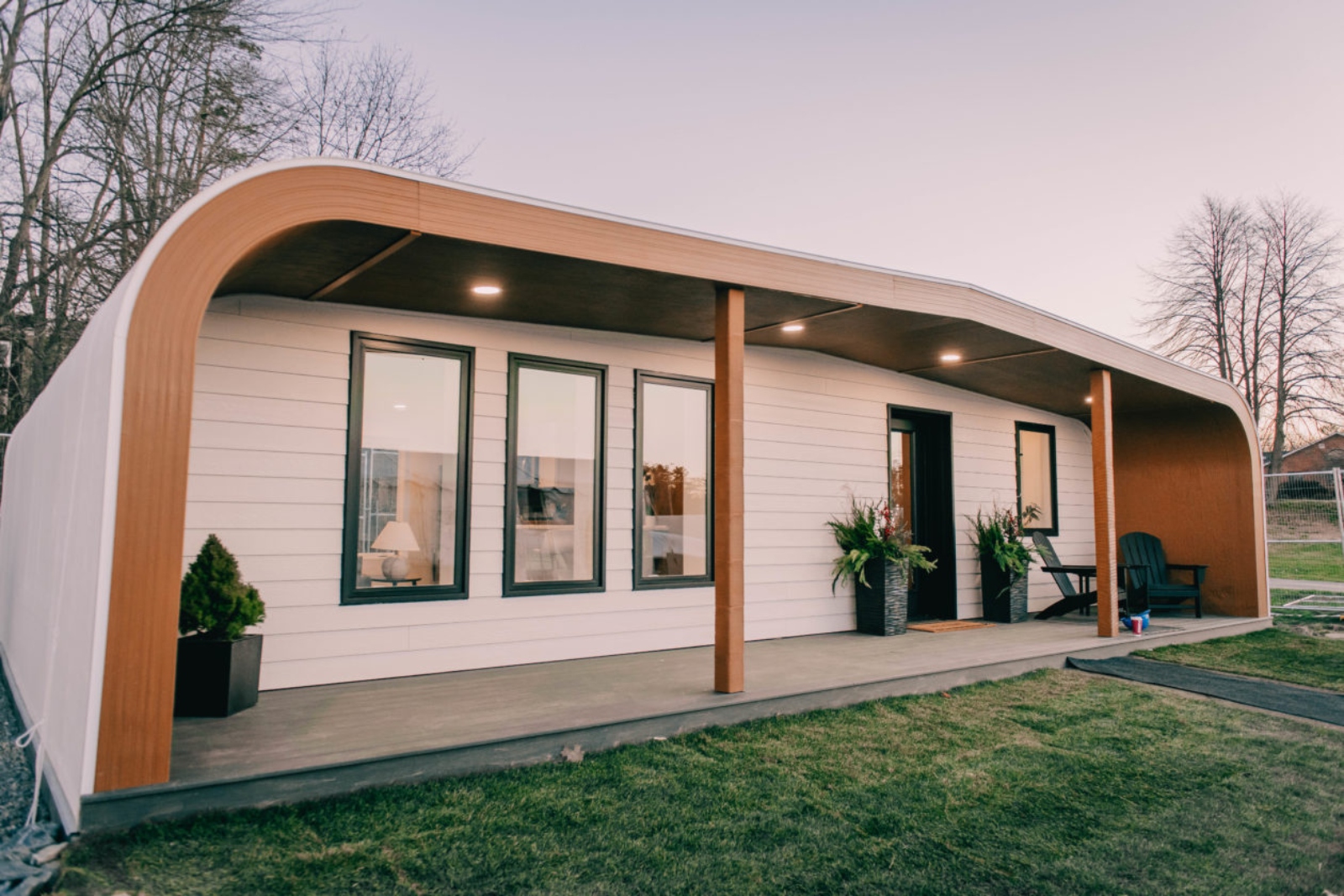
University of Maine
“This material is recyclable,” said Evan Gilman, the center’s chief operations engineer. “If in a hundred years this house becomes unusable, you could take the material, grind it up, and print another home or other structure or something else useful. It could be repurposed for the future.”
Mass timber, also known as cross-laminated timber, is also increasingly popular as a building material. Made from pieces of wood laminated or nailed together, it is in some ways stronger than steel and concrete. And because the wood stays intact for the life of the building, it will sequester carbon for decades or even longer — potentially converting buildings from carbon sources to carbon sinks.
While research and development are on the upswing, scaling up from lab-made samples to mass production is the next and bigger hurdle. In fact, the gap between the discovery and successful marketing of a new product or process is known by venture capitalists as the “valley of death.” The U.S. does “very well at the R and D phase, and we have some commercial-scale production,” said Melanie Tomczak, BioMADE’s chief technology officer. “But it’s that middle, that pilot-plant production, that we don’t have. There hasn’t been incentive at that scale.”
There is also concern that bio-based products are susceptible to “greenwashing” — overselling their environmental bona fides — or to unintended consequences. Eighteen years ago, for example, the federal government greatly expanded a program to encourage biofuel production, mostly from corn, as a way to cut down on CO2 emissions from fossil fuels. Now more than a third of the U.S. corn crop goes to biofuels. One recent study, though, found that the federal incentives to grow corn for ethanol led to land conversion to cropland, which caused the release of greenhouse gases into the atmosphere, offsetting gains from the program.
And while building with mass timber could well be more sustainable than building with steel and concrete, depending on a number of factors — including how long the beams are kept intact — the demand for mass timber may lead to more logging.
While a true bioeconomy is a long way from fruition, increased attention to and funding of the field is creating momentum. A large part of the battle may simply be public awareness. “We need more early adopters to drive the economy of scale,” said the University of Maine’s Gilman. “The technologies exist, but they are not being utilized because they aren’t as efficient yet, or people just don’t understand the potential. We need momentum, some early adopters to buy into it. That will really drive development.”