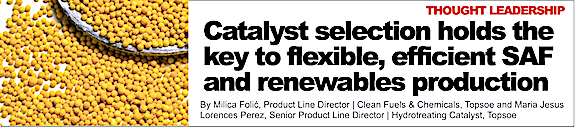
By Milica Foli?, Product Line Director | Clean Fuels & Chemicals, Topsoe and Maria Jesus Lorences Perez, Senior Product Line Director | Hydrotreating Catalyst, Topsoe
Special to The Digest
For over a century, refineries have mastered the art of processing fossil fuels. However, the emerging field of converting renewable feedstocks into transportation fuels, such as Sustainable Aviation Fuel (SAF), presents some novel technical challenges both for traditional refineries looking to diversify and/or revamp, and for newcomers, write Milica Foli? and Maria J. L. Perez, Topsoe.
Addressing these challenges requires customized solutions tailored to the specific needs of each refinery or greenfield facility. Factors such as the type and quality of the end product, the nature of available feedstocks, and the ease of integration with existing refinery units (in the case of revamps) must all be considered.
Ideally, solutions for processing renewable feedstocks into SAF should offer some feedstock flexibility, enabling refineries to produce clean fuels from a diverse range of inputs including vegetable oils, animal fat, used cooking oil, pyrolysis oil, and so forth.
Central to success are catalysts. For instance, guard catalysts are essential as they manage contaminants and ensure the longevity of the processing cycle. Given that renewable fuels typically have a higher cloud point than fossil fuels, dewaxing also becomes critical. Dewaxing catalysts that enhance the cold flow properties of renewable fuels through selective isomerization while minimizing yield loss are vital and will be explored further in this article.
Considerations when hydroprocessing renewable feedstocks
Hydroprocessing renewable feedstocks can be complex. From process design to choosing the optimal catalyst technology, there are many factors to consider.
The first critical step is to decide exactly which product you want to end up with: renewable diesel or SAF? For instance, if you are considering diesel, what are the right specifications to aim for? EN590 (regular diesel) or EN15940: 2016 Class A (HVO-100)? These choices are critical because they have a direct bearing on process design and the choice of catalyst solution.
Importance of catalyst technology
Transforming each renewable feedstock into a particular type of transport fuel demands the application of specific catalysts. For example, carefully designed guard beds are required to handle the high levels of contaminants such as phosphorus, sodium, and silicon present in some renewable feedstocks.
Selecting the right hydrotreating catalyst is critical for choosing the optimal reaction pathway (HDO vs. decarboxylation) as the catalyst has a huge effect on the yield structure. In order to optimize yield structure and cycle length, one of the focus areas at Topsoe, for example, has been to develop a wide selection of hydrodeoxygenation catalysts. The market will be moving towards processing more difficult feedstocks (i.e., tallow, biomass, plastic) that contain higher levels of contaminants. Additionally, it is predicted that existing diesel hydrotreating plants will be converted into renewable units with operational limitation that we need to address, for example low pressure.
The feedstock we are using today might not be the renewable feedstock you use tomorrow – especially when using unconventional feed. New generations of renewable feedstocks will impact catalyst performance.
Hydrotreating triglycerides produces normal paraffins. As these molecules dictate the cold flow properties of the resulting product, dewaxing might be needed. Topsoe has developed a wide range of dewaxing catalyst technologies for both sweet and sour production modes. Each catalyst has a particular attribute, such as high yield, high tolerance to nitrogen or effective end-point reduction. Factors such as the type of feedstock, the specifications of the end product, and the unit layout, all play an important role in selecting the right combination of catalyst technologies.
Dealing with undesirable wax components
From a conventional fossil fuel, diesel contains wax components (n-paraffins) that are valued for their high cetane number. However, when diesel gets cold, these wax molecules crystallize, potentially blocking fuel filters and lines, especially in colder climates. This issue is significant in producing renewable diesel from biomaterials, which can contain substantial waxy n-paraffins that may remain solid even at +20 °C after hydrotreating.
Several methods exist to address undesirable wax components from the conventional refinery, but they are often not economical. Feedstock undercutting, for instance, removes the heavy tail of the feedstock containing long-chain n-paraffins, but also reduces diesel yields. Kerosene dilution prevents wax molecules from affecting diesel quality but represents a missed revenue opportunity, as kerosene can be sold as jet fuel. Meanwhile, additives are expensive and generally ineffective for improving the cloud point. Despite these drawbacks, however, refiners have relied on these costly methods due to the limitations of conventional dewaxing options. Thankfully, better solutions are now readily available.
Renewable feedstocks require dewaxing to a whole new degree, because the cloud point after hydrotreating increases dramatically (to +24°C). Depending on specification of the diesel, the cloud point can be as low as -26°C and even lower for renewable jet fuel (-40°C). Catalytic dewaxing is widely established in the industry for this kind of application.
Dewaxing by Cracking or Isomerization?
Catalytic dewaxing ensures that oil products, remain liquid at specific temperature ranges to meet essential cold flow requirements. This can be achieved through two methods: cracking long n-paraffins into shorter ones or isomerization.
Conventional dewaxing catalysts improve cold flow properties by shortening n-paraffin chain lengths through cracking or a combination of cracking and isomerization. However, their significant cracking functionality often results in lower boiling point fractions, leading to yield loss and performance issues in winter conditions.
Isomerization-based dewaxing, on the other hand, maintains the number of carbon atoms in the hydrocarbon chains while rearranging their positions. This approach significantly enhances yields of higher-value diesel with on-spec cold flow properties, making them commercially attractive.
New-generation catalysts, such as TK-930 D-wax™ and TK-920 D-wax™ , now offer a drop-in solution for improving cold flow properties in most existing hydrotreating units. These catalysts are highly isomerization selective and provide much lower diesel yield loss than conventional dewaxing catalysts which have a significant cracking activity.
TK-930 D-Wax™ utilizes a zeolite structure with selected base metals that are resistant to sulfur, nitrogen, hydrogen sulfide, and ammonia in sour environments. These base metals ensure exceptional hydrogenation activity, supporting hydrodesulfurization, hydrodenitrogenation, and hydrodearomatization reactions while TK-920 D-WaxTM is a noble metal dewaxing catalyst suitable for sweet mode operation.
The zeolite structure acts as a molecular sieve, allowing only long n-paraffins to participate in the isomerization process.
This catalyst enables refiners to meet cold flow property regulations with maximum yield, without the need for costly revamps, layout changes, or additional equipment.
Conclusion
The production of SAF and other renewable fuels presents unique technical challenges that differ significantly from traditional fossil fuel processing. Addressing these challenges requires a flexible approach, tailored to the specific needs of each producer. Key considerations include managing contaminants and maintaining optimal cold flow properties.
Catalyst selection plays a crucial role in overcoming these hurdles. Advanced catalysts, such as TK-930 D-Wax™ or TK-920 D-Wax™, offer innovative solutions for dewaxing, enhancing cold flow properties, and maximizing yields without the need for extensive modifications to existing infrastructure. By leveraging the right catalyst technologies and process designs, refineries and greenfield renewables producers can efficiently convert a wide range of renewable feedstocks into high-quality, commercially viable fuels.
More on Topsoe at topsoe.com.