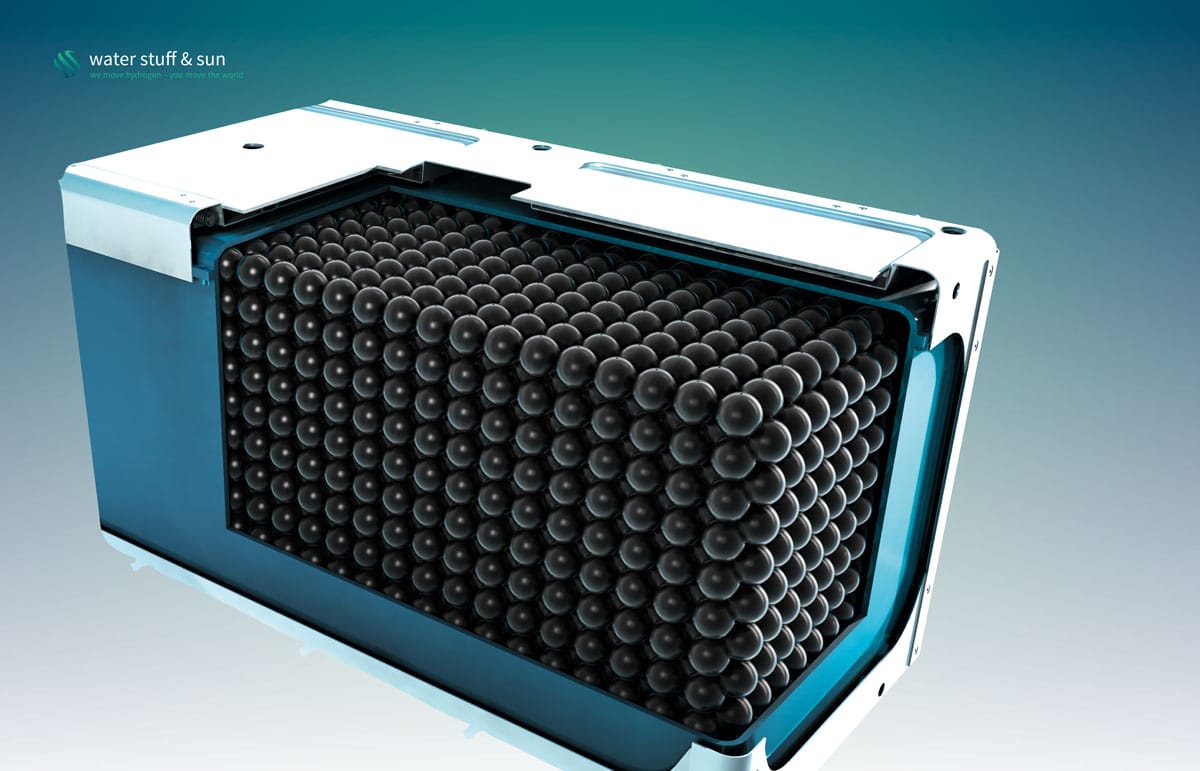
Interview with Thomas Korn, CEO of water stuff & sun
Startup company water stuff & sun has developed a novel technology that is designed to provide a safe and easy way to store hydrogen. The solution’s key component is its microvalve system. A pressure regulator controls the release of hydrogen progressively from 1,000 bar down to just a few bar. H2-international spoke to Thomas Korn, CEO of water stuff & sun, about how it works and the challenges encountered.
H2-international: Mr. Korn, the storage and refueling of hydrogen is a challenging issue. How do you solve that problem?
Korn: As it stands, the storage of hydrogen in conventional compressed gas tanks is complex and expensive. There is a trade-off between performance, safety and cost. We have a surprising solution to this: Instead of using a small number of large cylindrical tanks, our technology allows us to store the same amount of hydrogen in multiple spherical carbon-fiber vessels the size of a tennis ball. The silicon microvalve system, which is built into every pressurized ball, means that all the vessels act identically and in unison, just like a large tank. The expense involved in ensuring the safety of hydrogen stores can be significantly reduced if the energy is split into multiple small vessels. As a result, we save almost half the carbon fiber material compared with a standard pressurized tank. We call these ball-shaped high-pressure storage vessels Sfeers.
They allow hydrogen cells to be scaled as required and integrated into hydrogen batteries of any shape. Green hydrogen can thus be used in a variety of motive and stationary applications such as trucks, drones and airplanes. The next generation of these energy stores will be 95 percent lighter and up to 30 times cheaper than lithium ion batteries – while still carrying the same amount of energy.
Fig. 2: Doing the rounds: a Sfeer ball at the EES trade fair in Munich
How does the hydrogen battery work?
Hydrogen batteries are low-pressure hydrogen tanks containing Sfeers which are filled at up to 1,000 bar. The hydrogen battery enclosures are designed for low pressures and can therefore be perfectly adapted to the available installation spaces in a wide array of mobility products. When hydrogen is extracted, the pressure in the hydrogen battery enclosure decreases and activates the microvalve system in all the Sfeers once the pressure drops below a mechanically programmed ambient pressure range. These then release hydrogen, together providing the energy required for a hydrogen engine or a fuel cell.
The pressure in the hydrogen battery rises again above the pressure activation level that is set during the manufacture of the micromechanical components. Once the pressure level has been reached, all the microvalves close. The pressure in the battery stays constant or reduces further if the consumer withdraws more hydrogen. The activation pressure is set to the supply pressure of the consumers. The hydrogen battery can be thought of as a low-pressure tank, but with the capacity of a high-pressure tank.
The concept increases the safety level while at the same time reducing the amount of material used. Since their highly adaptable shape means they can make best possible use of the available space, hydrogen batteries outperform conventional pressurized tanks in terms of volumetric and gravimetric power density.
Microvalve technology has its origins in satellite technology. How is this technology produced?
Satellites have a gas propulsion system that secures their position within the communication window. Even in the early days, industrial developers started to use microsystem technology to regulate gases due to financial pressure to make ever smaller and lighter satellites. Our innovation centers on the development of micromechanical switching elements that don’t need electrical energy for their control; instead they are controlled passively by the ambient pressure. As in semiconductor engineering, highly industrialized manufacturing processes are used that can create thousands of identical parts on large silicon wafers. Valves, gas channels and the five-stage pressure regulator are produced and joined in four silicon layers. All chip components are built into a space measuring 4 x 4 x 2.5 millimeters (0.16 x 0.16 x 0.1 inches).
How did you come up with the idea of spherical high-pressure vessels?
The technology was invented by Prof. Lars Stenmark, who taught microsystem engineering in the Ångström Laboratory at Uppsala University and who had already applied earlier inventions to the aerospace industry. When he told me about his hydrogen storage invention, I was all for it. A physical hydrogen storage vessel that combines two existing technologies and resolves the trade-off between safety, cost and performance in hydrogen tanks – we couldn’t resist and founded the company water stuff & sun in January 2017.
Fig. 3: A view of the lab shows the test setup for microchip evaluation
Is there already a prototype?
We have already produced and tested prototypes of switching valves and the key element of the valve system – the pressure regulator – in the clean room of the Ångström lab in Uppsala. We have also put a carbon fiber Sfeer prototype through a burst test and validated our simulation model with the results. At the moment we are building the first system prototype of a hydrogen battery with three Sfeer cells. The prototype and its use in a micromobility application will reach technology readiness level 5 in the first half of 2024. At that point we’ll start to develop hydrogen batteries for specific mobility products with several manufacturers and go on to industrialize them in the next stage. There is a great deal of interest from industry. For example, we have already submitted a joint funding project with an aircraft manufacturer and the German Aerospace Center. We are working with our partner Keyou to develop hydrogen batteries for converting and retrofitting trucks and buses. Additionally, we’ve managed to stimulate interest from a mining machinery manufacturer and a truck OEM.
Returning to the refueling process: Am I right that you are intending to swap the tanks?
Hydrogen batteries don’t need to be refueled in the vehicle; they are exchanged at swap stations or, in the case of small applications, they can also be exchanged by hand. That way, refueling can take place quickly and cost-effectively. The empty hydrogen batteries are refilled at central compressor stations and returned to the swap stations. The low operating pressure and the limited quantity of H2 in the hydrogen battery enclosure makes this ease of handling possible. In comparison with conventional high-pressure or liquid hydrogen refueling stations, the expense and complexity are significantly reduced, which in turn lowers the capital and operating costs and thereby also the hydrogen price. For heavy-duty vehicles, for instance, with hydrogen, several hundred liters of fuel energy equivalent need to be compressed, cooled and transferred. By simply swapping the hydrogen battery, the process can be completed in just a few minutes.
The financing required will be considerable. What are the next steps for your company?
The need for capital in a tech startup is always an issue – it’s a continuous process. We have just started a new financing round in which our existing investment partners, such as the investment arm of Kreissparkasse Esslingen-Nürtingen, or ES Kapital for short, the company Besto, run by the entrepreneurial Beyer and Stoll families, and machinery and tooling factory Nagel, have already registered an interest. I would refer to them as relatively down-to-earth, regional investors that have been involved from an early stage. The plan is to invest the new cash in the development of a prototype in the motive application area, as mentioned earlier, among other things. The raw materials for the production of semiconductor chips are all affordable. Carbon fiber and silicon are readily available on the market. That is an advantage in terms of further scaling. If everything goes according to plan, we will see the first of our batteries in a vehicle or aircraft by 2025.
Fig. 4: The H2 battery should be quick and easy to swap in and out of a truck
When and how will the market for your solution evolve?
The transformation of energy systems is well under way. Infrastructure for natural gas- and oil-based fuels is being replaced by hydrogen and liquid hydrogen derivatives such as ammonia, methanol or synthetic fuels. The competition for technology leadership and, ultimately, energy leadership began long ago. In China and the USA, many billions of euros are now being invested in hydrogen technologies and their infrastructure; we Europeans are attempting to counter this with the Green Deal. Hydrogen projects are sprouting up all over the place. As far as we are concerned, the market has already started; we’re currently concluding cooperation agreements with initial vehicle and machinery manufacturers.
Where will the first market be that manages to develop?
We need to take a multitrack approach and are therefore also looking at the USA and the Arab world. The country that achieves the lowest hydrogen prices by investing will attract a lot of companies and investment. In the EU and Germany I hope that the greenhouse gas quota gives us an instrument that is competitive.
You won a prize at the World CleanTech StartUPs Awards, otherwise known as WCSA 2023. What particularly impressed the judges?
Firstly, the award as a platform is a very interesting network in itself. Applications for WCSA 2023 were invited by ACWA Power in strategic partnership with Dii Desert Energy and the French institute for solar energy CEA-INES, among others. The judging panel recognized the transformative potential of the hydrogen battery. The innovation could create an efficient and flexible infrastructure for H2. The electricity costs for hydrogen production from renewables are very low in Dubai. That’s why ACWA invited us again at the end of 2023 to present our solution locally. That will be extremely exciting.
In November we received two awards at the Global EnergyTech Awards: the prize for the Best CleanTech Solution for Energy and a special prize for Best Stand Out Performer. We were the only winners from Germany. That helps.
Interviewer: Niels Hendrik Petersen
Fig. 5: Thomas Korn
Thomas Korn has been working in the hydrogen field since 1998. The engineer’s experience includes work at BMW on fuel cell development. In 2015, he co-founded the hydrogen startup Keyou in Munich. The startup water stuff & sun was launched in 2017 in Unterschleißheim, Bavaria. The fledgling company now has 15 members of staff and a branch in Uppsala, Sweden.