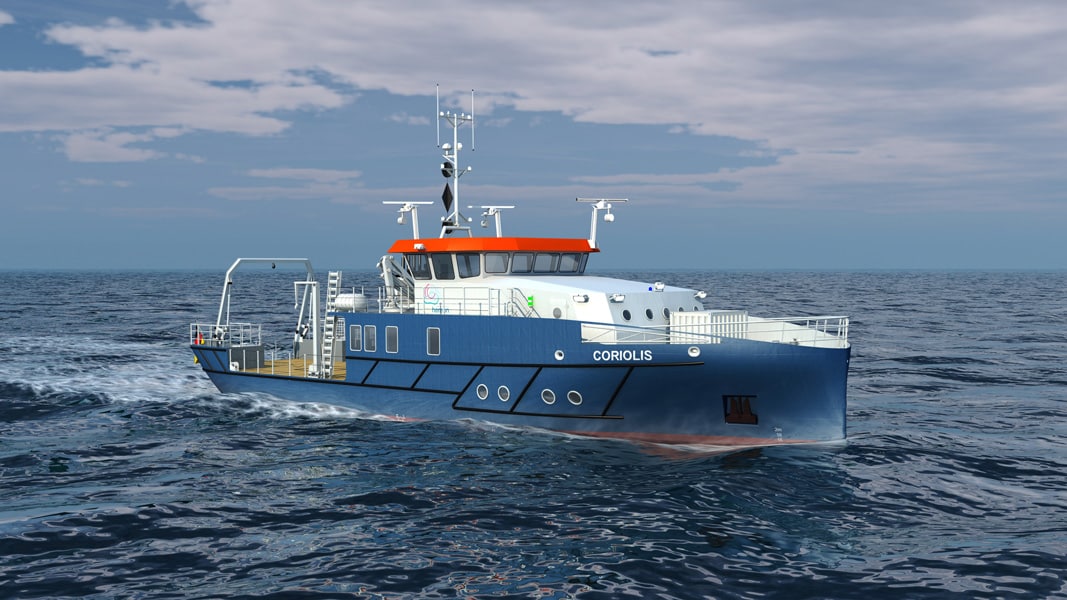
Zero-emission power system for a river and coastal vessel
Shipping is responsible for roughly 3 percent of all carbon dioxide emissions around the globe. The International Maritime Organization or IMO therefore set itself the goal of at least halving this figure by the year 2050, relative to a 2008 baseline. Due to the high power requirements and the large distances traveled by ships, fully electric solutions are only possible in isolated cases. Hydrogen and its derivatives are therefore attracting increasing interest from the maritime industry because of their potential to greatly reduce ship emissions. The challenge in this sector is, firstly, how to store the hydrogen on board safely in a minimal amount of space and, secondly, how to engineer the overall energy system to meet various requirements while optimizing its control.
The Hitzler Werft shipyard in Lauenburg, Germany, is currently building the Coriolis research vessel for the Helmholtz-Zentrum Hereon research center in Geesthacht. The ship will be fitted with a diesel electric power system in addition to batteries and a hydrogen system. The latter was designed by Hereon together with the DLR Institute of Maritime Energy Systems and the engineering consultancy Technolog in Hamburg.
Hydrogen system lab on board
The hydrogen system lab – H2SL – is designed to be a hydrogen system that is spread across the vessel. The main components are a metal hydride tank, which was developed by Hereon, and a low-temperature proton exchange membrane (PEM) fuel cell. Accompanying these are various pieces of peripheral equipment, such as a bunker station for hydrogen, a tank connection space at the metal hydride tank and two vent masts.
For a comparably small vessel such as the Coriolis, whose length is just under 30 meters (100 feet), extremely careful consideration is needed when arranging the components. One of the reasons for this is because there are no binding regulations yet that govern the use of hydrogen on board.
The definition of hazardous zones and the distances that need to be maintained between ventilation facilities come from the IGF Code, which regulates the handling of low-flashpoint fuels in shipping and has been primarily used for liquefied natural gas up until now. The code does not yet take into account the special properties of hydrogen, for instance its much higher volatility compared with LNG. Among other things, this evident in the size and shape of the hazardous zones (see the spherical hazardous zones around the vents and air inlets). Work on the IGF Code is currently ongoing to extend its scope to include the use of hydrogen.
The tank system, consisting of an actual metal hydride tank and the mandatory inertable tank connection space, will be built on a 5-foot container base plate and have around half the height. In addition to the weight of the metal hydride itself, the overall weight is made up of the steel tank shells, pipework and, in particular, the pressure vessel of the tank connection space. The overall system volume of around 4 cubic meters (140 cubic feet) and an overall system weight of 5 metric tons mean that the tank system stores approximately 30 kilograms of hydrogen.
This allows the fuel cell to supply the ship with roughly 500 kilowatt-hours of green energy. That said, this can only happen if the bunkering of green hydrogen is actually possible and permitted – a challenge in itself, as initial exploratory talks with port authorities and hydrogen producers have shown.
Prior to the shipyard tender, the energy requirement for craft propulsion was ascertained at SVA Potsdam using a model test and subsequently scaled up. The shape of the Coriolis is optimized for operation at low speed as this matches the primary operating profile of inshore journeys (see fig. 3).
Due to the low power requirement for creep speed, the fuel cell, which will have a rated electrical power of around 100 kilowatts, can be used in combination with the battery for numerous monitoring activities and in the other operating states of the Coriolis e.g., during layovers, without having to switch on a diesel engine. As well as the propulsion system, the electrical consumers on board also need to be supplied, although these only require a fraction of the power needed for propulsion.
Metal hydride tanks
From Hereon’s perspective, the following properties make metal hydride or MH tanks attractive for a range of maritime applications:
- Moderate loading pressures of well under 100 bar at operating temperatures below 100 °C
- Cold start of a MH tank possible in principle even at temperatures below 0 °C (Hereon EP 3 843 190)
- By the very nature of MH tanks, the hydrogen is chemically bound meaning the tanks cannot suddenly release large quantities of hydrogen, which is a significant on-board safety advantage.
- The low loading pressures allow a flexible structural form which makes it easy to adapt to the shape of the ship à saves space. Today’s pressurized hydrogen tanks take up a lot of room, especially on small vessels, which reduces valuable cargo space.
- The high weight can even be advantageous in certain applications, e.g., for sailing ships where it can be used instead of the obligatory “deadweight” ballast for stability.
Research in the H2SL
Hereon and DLR are working together to investigate which types of ship are best suited to the combination of a low-temperature fuel cell and a metal hydride tank for the propulsion system. The goal of the two research institutes is to create a guiding principle that enables the Coriolis energy system concept to be adapted and integrated easily into other ships and types of craft.
The H2SL offers many more opportunities to pursue innovative research approaches in addition to facilitating zero-emission operation. Hereon and DLR are planning an intensive program of research using the power system and are expecting to gain valuable knowledge and real-time data on relevant research issues. This will be made possible by running the H2SL in a real maritime environment with the option to access operating data remotely online and immediately adjust the control parameters. The effects of these changes will then be the subject of further study.
DLR will develop a digital twin of the hydrogen energy system based on the operating data in order to produce a continuous record of the system status, optimize the system control and derive feedback for the operation.
What’s more, the information should allow operational strategies to be developed for the Coriolis’ hybrid energy system. The variation in energy sources, i.e., battery, fuel cell and combustion engine, creates a high degree of flexibility with regard to operation in a wide range of energy consumption scenarios. The goal is to achieve an optimal balance in relation to fuel consumption and operating costs through intelligent load sharing for a wide variety of traveling and loading states.
A benefit of carrying out this kind of investigative work on a research vessel is that strategies developed from theoretical principles can be transferred directly to the energy management system, allowing them to be swiftly validated during operation.
Hybrid energy systems are being built into ships with increasing frequency. The knowledge gained from sailing the Coriolis will supply valuable information in future that can also be transferred to other types of craft and thus contribute toward reducing emissions in the maritime sector.
Authors: Klaus Taube, Hereon, Geesthacht, Volker Dzaak, Markus Mühmer